2D printing is so 2015: Canon shows R&D tech that prints real-looking textures (and great sci-fi/horror props ;-)
posted Monday, September 21, 2015 at 9:40 PM EDT
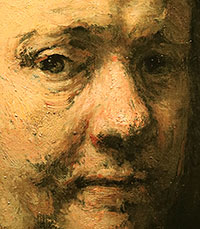
I still have some things I'd like to write up from my visit to Canon's Expo 2015 in New York the week before last, and one of the most interesting things I saw there was what Canon had been billing before the show as "Textural Printing." At the show itself, it was called Super Creative Printing, but I think the Textural moniker is a bit more descriptive.
3D printing has been all the rage lately (I have a 3D printer myself), but there's a huge gulf between 3D printing and the conventional ink-on-paper version. Ink on paper is representational, even photographic, but that's as far as it goes. Surface shape and texture can only be portrayed as seen by the camera, from a particular perspective, with a particular lighting.
3D printers on the other hand are oriented towards creating coarse-grained structural shapes with very little attention to color or surface finish, other than trying to minimize the visible layering seen with most technologies. Printing more than a single color is a big deal, and only a very few can produce a full range of color, but still with no control over surface finish or texture.
Canon's out to change all that...

Somewhere between photo prints and 3D structural shapes, there's a whole world of texture, translucence and fine-grained surface structure. This is the ground that Canon's exploring with Textural Printing.
Textural Printing gives you an idea of what the technology is all about, namely the ability to reproduce surface textures and to some extent the balance between light absorption and reflection that gives many real-world objects their unique appearance. Another word for it might be "2.5D printing", though, as it's really a kind of 3D printing technology, albeit one that's focused much more on color and surface finish, and not designed to create large 3D structures. It seems the tech can also vary the finish from full-gloss to matte, another important characteristic of real-world surfaces.
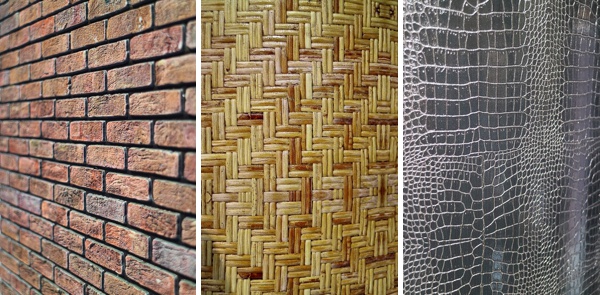
The heart of the technology is an Océ inkjet printer, laying down CMYK (the four reflective primary colors of Cyan, Magenta, Yellow, and Black) UV-curable resins. Details were a little scant, but from what I could determine, it seems each layer is about 0.1mm thick. Basically, the printer lays down a layer of resin, cures it with a blast of UV (ultraviolet) light, then lays down the next layer on top of it.
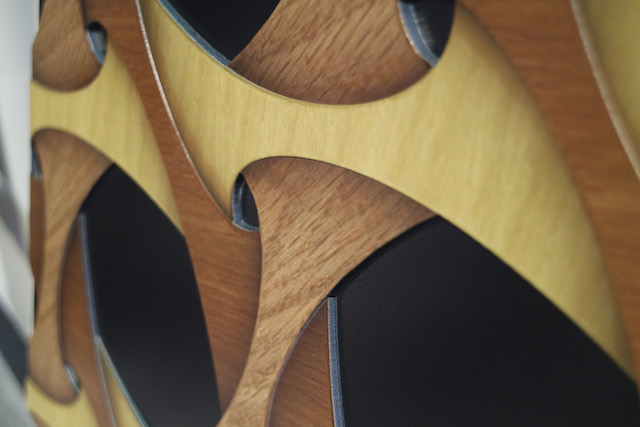
Again, Canon wasn't sharing a lot of detailed information about the tech, and only talked about CMYK resins, but from looking at the samples they showed, it's clear that there must be a clear resin as well, since the objects had varying levels of opacity. As mentioned above, this is significant, as it not only lets them reproduce translucent materials, but the appearance of many things you wouldn't think of as being translucent actually depends on light penetrating a little ways below the surface before being reflected back out again.
Overall, while the technology isn't yet capable of perfectly mimicking surface textures, a lot of the samples they showed that had been "printed" with it were fairly convincing if viewed from a little distance. I expect to see the technology advance beyond its already-impressive abilities, not only as the basic printing tech advances, but as Canon learns more about how to capture and characterize surface textures.
Besides surface textures, there were a few examples of more explicitly 2.5D output, that showed both the capabilities and limits of the technology.
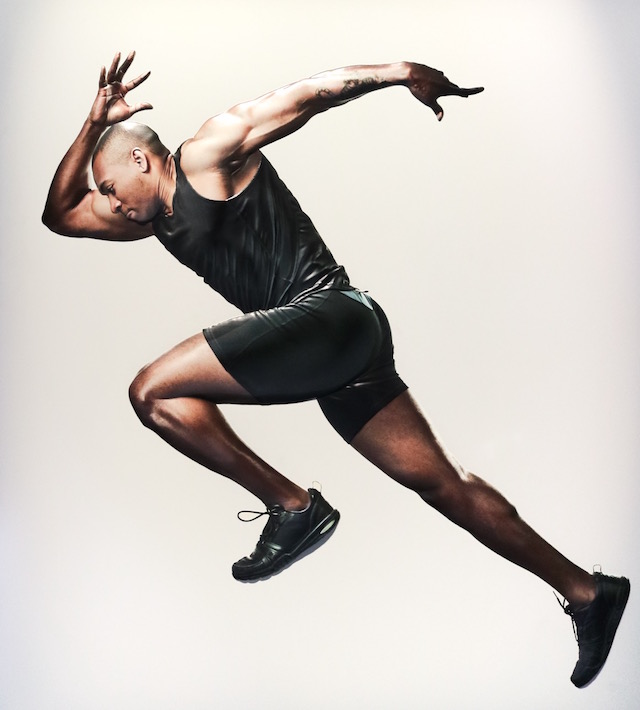
The showpiece of the exhibit was a huge, nearly life-size image of a runner, that protruded out from the substrate. I guesstimated its size at about 5 feet by 5 feet; which would makes sense if they'd used a 60-inch inkjet mechanism as the basis for the technology demo. It was quite striking; the image of the runner really projected quite noticeably from the background. Booth staff told me that the current height/thickness limit was about 22mm. I could really imagine images like this of favorite athletes being sold to sports fans. (In the US at least, life-size 2D prints of sports heroes are a significant business.) On the other hand, the technology will have to advance a lot to make such output affordable: it turns out the runner image took 3 days to create!
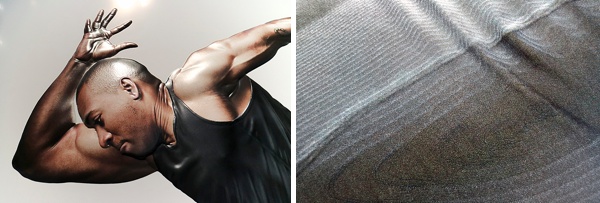
At a different end of the spectrum, some other output samples suggested to me that just because you can make something into a 2.5D print doesn't mean you should. There were a couple of family portraits on display that had been rendered in similar fashion to the runner, with the subjects' faces poking out from the background. I have to say I found theese a little disturbing, more like an effect from a low-budget horror movie than something I'd want to hang on my living room wall. (Eeyyaaahhh - Gramma Josie is coming back from the dead! :-)
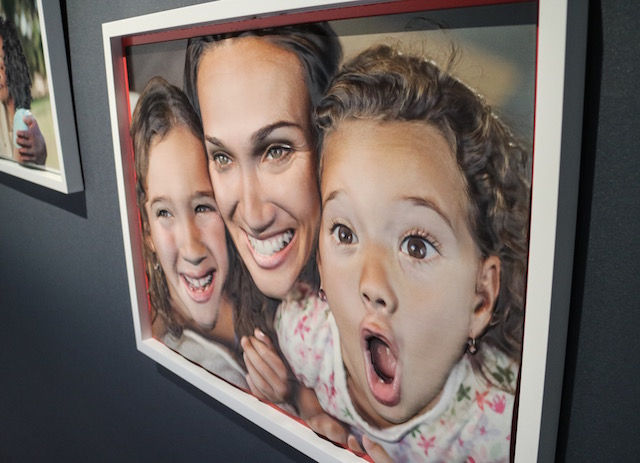
Seriously, though, as much as I might joke about the slightly ghoulish look of the family photo above, this is a really intriguing technology. I don't expect to see it implemented in an actual product anytime soon, but it's a direction we haven't seen before, and one that I can see finding a lot of application in the future. (Think: Custom wall coverings, product mockups, sports posters like the runner print above, and I'm sure many more. What uses could you think of for a technology like this?)
Given the nature of a show like this, a lot of technologies shown at Canon Expos never see the light of day - but I do hope this one makes it out to the real world at some point!