A deep look at the tech behind the Olympus 150-400mm super-tele zoom (Engineer interview!)
posted Thursday, March 4, 2021 at 1:05 PM EDT
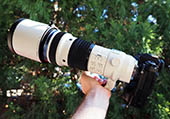
The Olympus M.Zuiko 150-400mm F4.5 TC1.25X IS PRO (that's a mouthful!) has been one of the most-anticipated lenses in recent years, offering an equivalent focal length range of 300-1,000mm in a single optic, thanks to its built-in 1.25x teleconverter. Its constant-aperture design delivers a maximum aperture of f/5.6 at the full 1,000mm equivalent, making it a surprisingly fast lens despite its super-tele reach. Even more remarkable is that it weighs only 1,875 grams (4.13 lbs) without its caps or hood. Add in an IS rating as high as 8 stops when paired with an E-M1X or E-M1 Mark III body, rugged all-weather design and excellent handling, and its $7,500 list price looks like a bargain. (For comparison, the single focal-length Nikon 600mm f/4 will set you back $12,300, a Canon 600mm f/4 runs $13,000, and even the Nikon 500mm f/5.6 goes for $3,600.)

By any measure, the 150-400mm PRO is an extraordinary lens, so I was eager to talk to the Olympus (now OM Digital Solutions Corporation) optical engineers about some of the tech that made it possible. To that end, I recently interviewed the engineers responsible for creating it and learned a lot about what went into its design and manufacture. It was a very interesting discussion for many reasons, one of which was that it had never occurred to me before that lens designers would take into consideration things like the center of gravity of a lens as part of its optical design.
My questions covered a range of categories; the following is just the order I happened to ask them in:
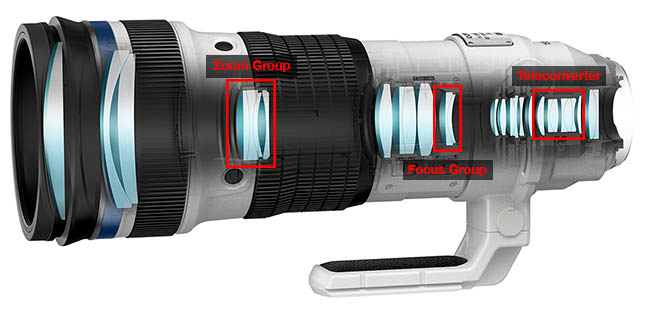
-- Weight reduction
DE: Weight reduction was apparently a huge focus of yours, and you used both magnesium alloy in the barrel and carbon fiber in the hood. How much did carbon fiber reduce the weight of the hood over conventional material? Also, mag alloy is lighter than aluminum, but I think it's stiffer as well. Did using mag alloy permit any fundamental differences in the mechanical design, or was it just a matter of shaving off grams due to the difference in weight? (I thought it was probably just a matter of the alloy being lighter, but it also occurred to me to wonder if the stiffer material might allow things like thinner cross-sections and tighter spacing between some components as well.)
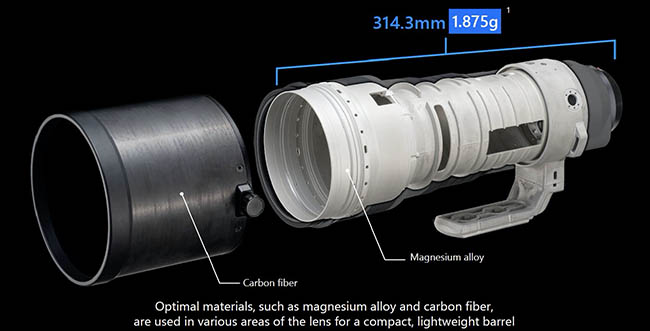
OM: One of the necessary characteristics of the lens hood is the resistance to breakage, which is a combination of the weight of the product itself, the external force being applied and the rigidity to prevent deflection when supported by hand. From this point of view, carbon fiber with its high specific strength and rigidity was selected as the best material for this product.
Compared to other materials with the same strength and rigidity, this product is more than 200 grams lighter, making it extremely light even with the hood attached, to enhance mobility. (Wow, 200 grams of weight savings just in the hood!)
Magnesium not only allows for weight reduction, but also contributes to miniaturization with its ability to make parts thinner, and by reducing the space between parts. (It seems my hunch was right; the stiffer alloy helped them shrink various parts.)
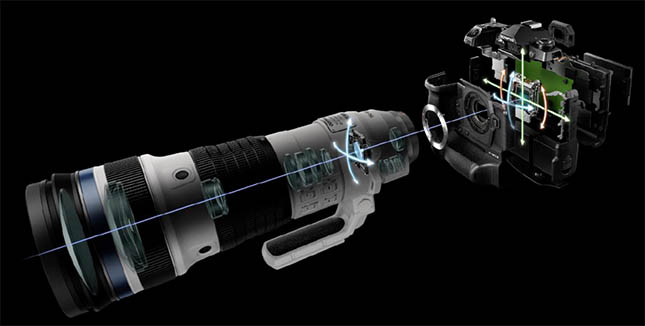
-- 8 stops of IS
DE: The 8-stop IS when used with the E-M1 III and E-M1Xbodies is extraordinary(!) Is this mainly the result of further improvements in gyro technology?
OM: The high-precision gyro sensor (jointly developed with Seiko Epson), which was first implemented in the E-M1X, is also incorporated in this product, and the algorithm has been optimized for telephoto use to achieve performance that exceeds that of conventional lens stabilization products.
Also, the lens image stabilization stroke (correction range) has been designed to be larger than that of conventional products to achieve a performance of 8 stops.
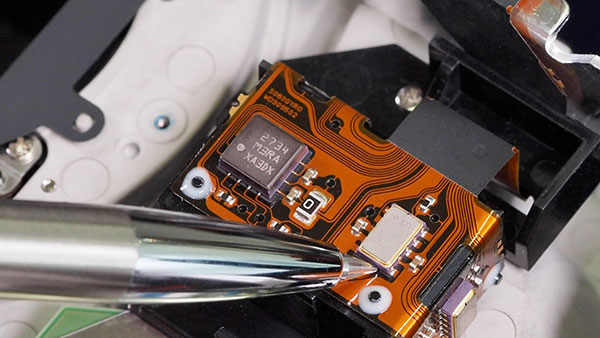
(It's interesting that this is still the same gyro from the E-M1X, that Olympus co-developed with Seiko Epson. Advances in gyro technology are the main reason we've seen IS systems get so much better in recent years. The keys to increased performance are reducing the amount of "noise" on the output signal, and controlling long-term drift. Basically, if you take any gyro and fasten it to the test bench, its output signal will still randomly fluctuate back and forth to some extent, and will also show some long-term drift, as if it was slowly rotating in one direction or another. Obviously, it's important that the gyro not tell the camera it's moving when it isn't, and the gyro signal needs to stay stable for as long as the longest exposure time you care about. Seiko Epson is one of the leading manufacturers of MEMS gyros in the world, and Olympus worked with them to push the state of the art beyond where it had been previously.
IS has always been an Olympus specialty, going all the way back to their C-2100 ultra-zoom, released in mid-2000. If you've ever wondered what goes on inside an IS system, check out my "Geeks tour of what makes IS work" article, where the head of Olympus' Mechatronics department dissected both in-body and in-lens IS systems down to their component parts for me.)

Back in 2016, their 300mm f/4 IS PRO lens used hand-selected gyros to deliver the then-incredible 6 stops of IS when coupled with Olympus IS-enabled bodies. With the E-M1X though, they and Seiko Epson pushed the envelope far enough that they could achieve 7.5 stops of IS with standard production components. This seemed to be some kind of absolute limit (see the next section below), but now they've managed to push things even further. To get an idea of just how insane this is, 8 stops of IS means that you can get sharp 1/4-second exposures in situations where you'd normally need to shoot at 1/1000 of a second.
-- Earth's rotation no longer an IS limit?
DE: Back when the E-M1X was introduced, we were told that its 7.5-stop IS was actually limited by the Earth's rotation(!) How was this overcome? Does the lens/camera combination make use of a compass to tell where the camera is pointing and thus how much Earth-rotation it's seeing? Or is it that it's able to detect the Earth-rotation component in the signal from the gyros, by looking for a consistent, slow drift that's at a lower, constant rate vs hand tremor?
OM: Although we have not been able to eliminate the effect of the earth's rotation, we have achieved high performance by minimizing other errors through high-precision gyros and optimization of algorithms. We cannot provide detailed information.
(Rats... :-) I'm not surprised they declined to give any details, but I'd love to know the inside story of what they're doing. The story about the Earth's rotation is actually a thing; if you do the calculations, over the course of a long enough exposure, a sensitive enough gyro will actually be responding to the rotation of the Earth. Thinking more about it as I'm writing this, I think the key here is that at longer focal lengths, handheld shutter speeds will go up high enough that 8 stops slower is still a short enough exposure time that you won't notice the rotation of the Earth. Still, I'd love to know some of the inner details...)
-- What's the IS rating when coupled with an E-M1 II or E-M5 III body?
DE: Related to IS, the 8-stop spec is when the lens is used with an E-M1X or E-M1 III body. What's the IS rating when it's coupled with an E-M1 II or E-M5 III body?
OM: It is not publicly announced, but the image stabilization performance is almost comparable to that of the E-M1X or E-M1 Mark III.
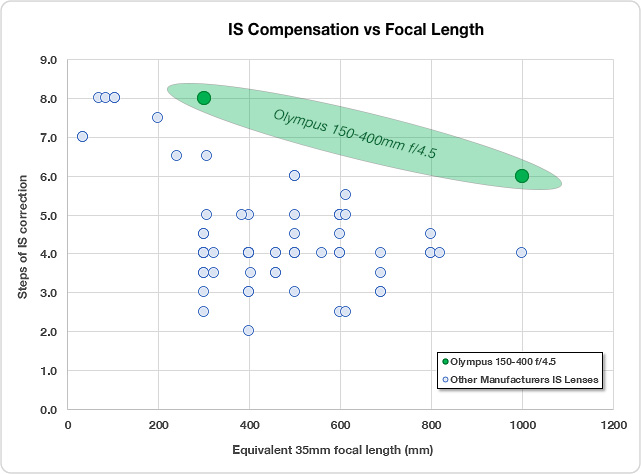
-- How does the switchable teleconverter work? Where does the TC group go when it's not in use?
DE: I'm very curious about the switchable teleconverter in the lens. How are you able to move the lens elements for the TC function in and out of the optical path with a switch? Where do the lens elements go when they're not in use? (That is, where/how are they positioned when they're in the inactive position?)
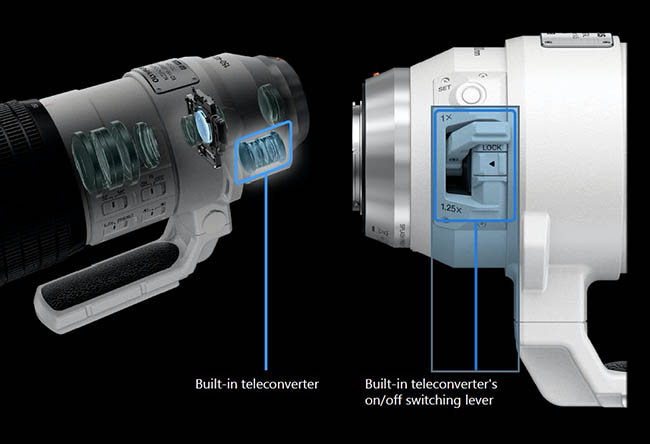
OM: The switching lever of the built-in teleconverter and the lens group of the built-in teleconverter are mechanically connected. The mechanical connection is important because it ensures a linear operating feel and reliability that is difficult to break.
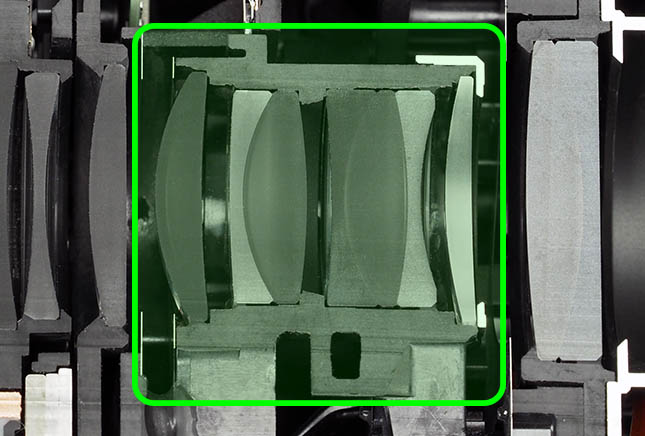
When the built-in teleconverter is off, the lens group of the built-in teleconverter is mechanically positioned off the optical axis (the part of the exterior that bulges out at the lower left when viewed from the lens mount side).
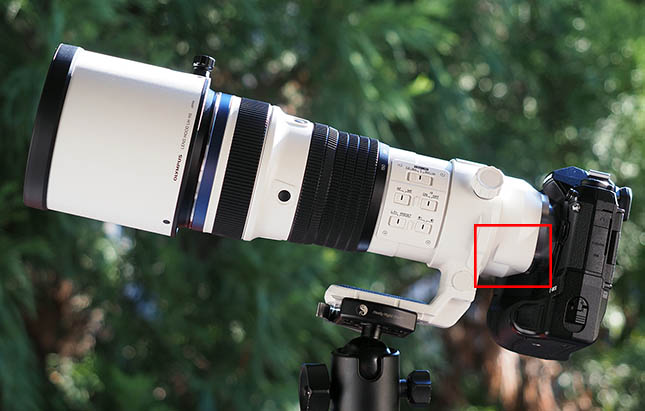
I'd wondered about that little bump, but it's smaller than I would have guessed would be needed to hide the teleconverter elements; they're smaller in diameter than I'd expected - but also much more complex optically. In both the first illustration above and the optical formula diagram below, we can see a total of 7 lens elements just in the teleconverter section.
-- What was the key to making the unusually large ED lens elements?
DE: The product briefing we received mentioned that one of the keys to creating this lens was a larger ED lens element than had been made before. What are the limitations in making large ED elements, and how were they overcome?
OM: The use of EDA lenses (Extra-low Dispersion Aspherical lens) with larger diameters than before greatly contributed to the smaller size and higher performance. The aspheric processing of EDA lenses involves pressing using a die, and since the pressing process is performed in the range of several hundred degrees Celsius where the glass becomes soft, control of heating and cooling is important.
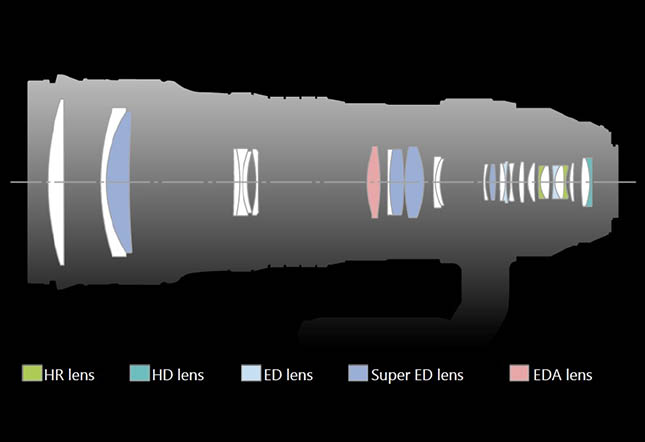
On the other hand, the glass material used for the EDA lens is a special low-dispersion glass, which has twice the coefficient of thermal expansion (twice the shape change due to thermal change) than ordinary glass materials.
Therefore, the larger the diameter an EDA lens is, the more likely it is to crack due to the temperature change (heating → cooling process) during the pressing process.
We have solved the problem of cracking and secured high aspheric accuracy thanks to our original molding machine, equipped with powerful heating and slow cooling functions, which can precisely control the mold at several hundred degrees Celsius within a range of ±1 degree Celsius.
Ah, this was very interesting to me! As they mention, aspherical lenses are made these days by heating glass blanks and then pressing them into highly-polished tungsten-alloy molds. I've known for some time that ED glass was more difficult to shape like this, but I had thought it was maybe just a matter of having a higher melting point or something similar. I didn't realize that the thermal expansion coefficient was twice that of conventional glass.
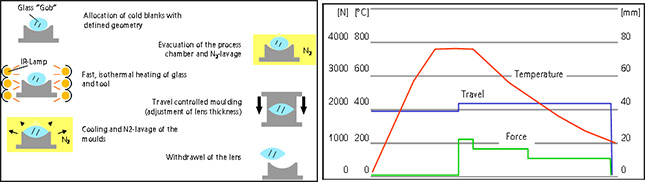
(Illustration composited from Wikimedia Commons images, cc-by-sa)
The tricky part with aspheric molding is that the glass shrinks as it cools. This means a couple of things. First, they have to design the molds to produce the correct final shape of the lens, after it's cooled and shrunk. Since thick parts of the lens shrink more, they need to make the mold cavities for those parts that much thicker than they need to end up, so they'll match the desired profile after they've cooled. The second consequence is that they have to be very, very careful about how they cool the glass back down after it's been pressed into shape. In particular, the thin parts of the lens will shrink less than the thicker parts, and the differences will add up even more the larger the lens gets. So molding very large aspheric elements is tricky, and much more so when using ED glass, because it shrinks twice as much as it cools.
Olympus' solution was to design their own molding machines with very precisely controlled temperature profiles. (I wonder if they might even have to maintain different temperatures between the center and edges of the lens molds? They didn't say this and it'd be highly proprietary if it's even possible, but when I think about the challenges of making large aspheric elements, introducing deliberate temperature gradients between the center and edges immediately comes to mind...)
-- Other key enabling factors
DE: Can you share any other key enabling factors that contributed to the development of this lens? It was announced an unusually long time before it eventually shipped. Were there manufacturing challenges that had to be overcome to be able to produce it? If so, what were they, and how were they achieved? It really seems like the 150-400mm is a whole new level of capability for Olympus optics; I'm sure our readers would be interested in any details you can share.
OM: We define this lens’ concept as “Unparalleled telephoto freedom”. We want our customers to feel the thought that we put into the concept of this lens, guaranteeing great operability that allows photographers to focus on the subject and the reliability to allow them to take photos in any harsh conditions. In both of these ways, we tried to develop a lens delivering overwhelming telephoto shooting experiences. To us, developing a 1000mm-equivalent f/5.6 lens while guaranteeing high-quality images with incredibly compact size was a big challenge.
One challenge in the optical design was finding the best position for the center of gravity for hand-held shooting. Thanks to the internal zoom mechanism, the change of the center of gravity as you zoom was reduced. In order to reduce the change of the center of gravity more effectively, we selected as small a lens unit as possible to move during zooming. We also designed the optics so that the position of the center of gravity can be as close as possible to the camera body for more comfortable handheld shooting.
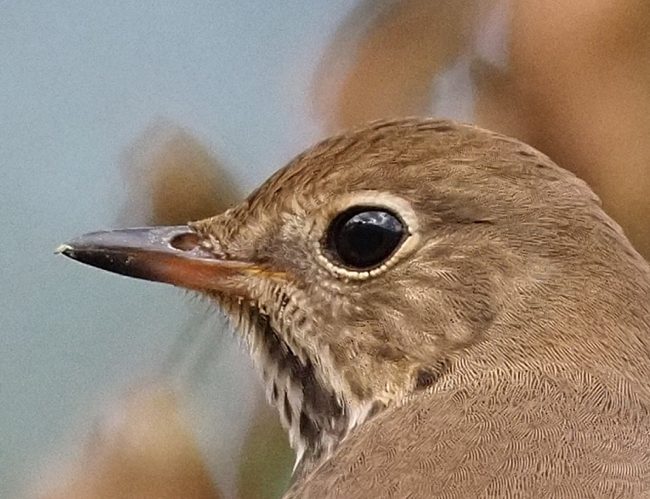
To the mechanical design team, downsizing and weight saving without compromising rigidity was the biggest challenge. On this lens, magnesium alloy and carbon fiber are used, and the team had to design parts with the correct material in as small a volume as possible. Of course, they did not give up any quality or reliability. This lens passes in-house drop tests and product life tests which are harsher than previous tests we used for other lenses.
Realizing the comfortable operability of a built-in teleconverter was a new factor that the engineers had to overcome. To the camera, using the built-in teleconverter is the same as using an entirely different lens. Therefore, the camera has to read the signal from the lens and change its settings quickly. Doing this smoothly without making a photographer feel uncomfortable was one of our new challenges.
It took us long time to start sales of this lens following the first announcement of development. However, a longer time was required for developing needed technologies and for prototype verification to increase the degree of perfection. The difficulty of developing the manufacturing process for the optical elements and the durability test process of new mechanical parts and so on required us to spend a longer time. We also repeated field tests by professional photographers many times for prototype verification, to improve the reliability as much as possible.
We know many photographers need this lens and we apologize for the wait, but we have now developed an attractive lens for all types of photographers.
I had suspected that manufacturing challenges were behind at least some of the delay. If I had to make a guess, I'd say that the large-diameter ED aspheric element was probably the cause of a lot of it (although they also pointed to mechanical design challenges as well). On many factory tours over the years, aspheric molding has always been portrayed as a primary challenge. The technique has been known and practiced for a long while now, but it's still fiendishly difficult to control, not only as lens elements get larger, but also in the case of lenses with large variations in thickness across their diameter. Manufacturability vs performance is always a tricky balance. There are lens designs I'm aware of that never shipped in enough volume to meet market demand, simply because they were too hard to manufacture. I'm also aware of at least one design that was dropped most of the way through the development process because the company involved realized they simply couldn't manufacture it with sufficient yield. In the case of the 150-400mm, it seems to have all worked out well, given how much the EDA lens element does for its performance and compact size.
-- Is the "Z-coating" nano-AR coating new?
DE: There are many different approaches to anti-reflective nano-coatings, and the image shown of the Z-coating in the briefing deck was unusual in that the coating looks like it's made of little spheres. Is this in fact different than previous Olympus nano-AR approaches? (I don't recall; were there nano-AR coatings in any previous lenses? Maybe this the first one?) I know that details of nano-coatings are very proprietary; everyone has their own "secret recipe" to make them. That said, though, can you share any further details about the Z-coating or its advantages? Does its specific structure make it easier to produce, or does it provide better characteristics than other approaches?
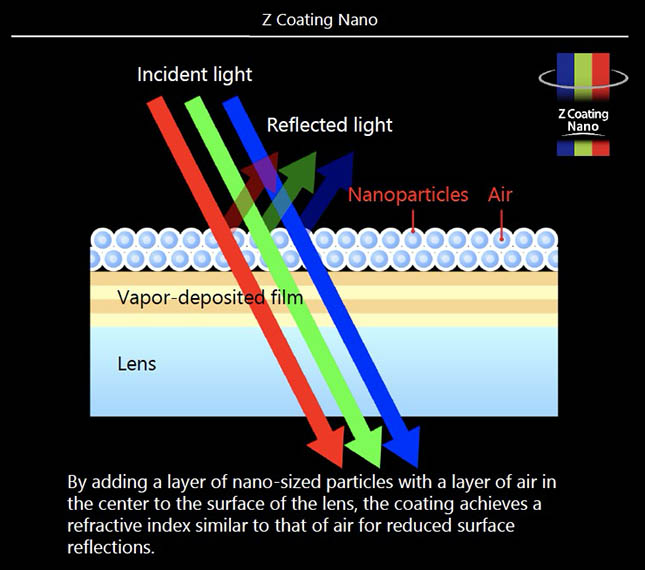
OM: The ZERO coating is a dichroic coating, a hard coating with a low surface reflection that can be used on the outer surfaces of the lens, while the Z Coating Nano is a coating that further reduces surface reflectivity by laying nano-level microscopic particles on the lens surface to have the same effect as ultra-low refractive index materials.
We think that its structure and properties are probably similar to those of other companies' nano-coatings. However, Z Coating Nano uses our original design and manufacturing methods to ensure the performance of low reflection and the quality of appearance.
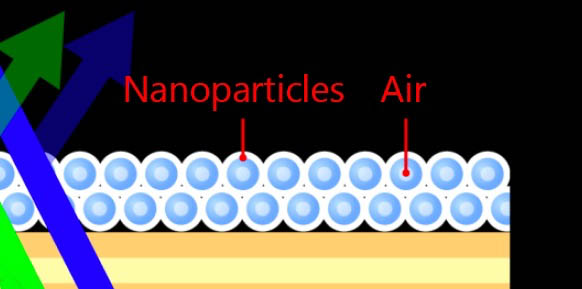
Nanoscale anti-reflective (AR) coatings are a relatively new development in lens manufacturing, although they're becoming much more common as more companies master the processes to create them. They're an interesting technology in and of themselves. What causes reflections from any surface is the abrupt change in refractive index between two materials. In the case of lenses, the two materials involved are glass and air.
The full story of how AR coatings work would be way too much to include here, but there are basically two different approaches. In one, the idea is to provide an intermediate layer or layers with refractive indices between those of glass and air, so there's not such a large step-change between them. Multiple smaller steps cause less reflection than a single larger one. The limitation of this technique is that it's hard to find substances with very low refractive indices (close to that of air), so beyond a certain point you're just stuck with what you've got.
The second approach uses multiple, alternating coatings of different refractive indices and thicknesses that deliberately cause inter-layer reflections that cancel out particular wavelengths or colors of light. Each pair of coatings can only cancel out one wavelength, but if you stack up enough of them, you can get pretty good anti-reflection across the spectrum. (These color-selective AR coatings are why you see colored reflections when you look in the front of a lens.)
Lens manufacturers use a combination of both approaches, but before nano coatings, there was still a good bit of reflection happening within the lens that caused lens flare and loss of contrast.
Nano coatings take the first approach mentioned to a logical extreme and actually can provide a very smooth transition between the glass and air. They do this by creating a mix of the coating material and air itself(!) There are many ways of making them, but the basic idea is the same across the board: Lay down nano-particles of some substance in a way that starts with a solid layer and then gradually has more and more air mixed in with it the farther you get from the surface of the glass. Because the particles themselves are much smaller than a wavelength of light, the light just sees a gradual change in refractive index, almost entirely eliminating reflections.
The one drawback of nano coatings is that they're very fragile and easily scratched, which makes sense given how thin and spidery the outermost layer of the structure is. This means they can only be used inside a lens, but that's where the bulk of the flare-causing reflections are going to happen anyway, given the many glass/air transitions in modern lens designs. (We have advanced AR coating technology to thank for many modern lenses; years ago, optical designers could never think of having 20 elements in a lens; the reflections between them would make for horrible flare and low contrast. Coating technology really opened up what designers could do, and is a big part of why today's lenses are so much better than those from even 10 years ago.)
I was intrigued by Olympus' approach because the microscope image above shows the nano-particles more like small spheres than other coatings I'd seen in the past.
-- Infrared-reflecting coating on the lens barrel
DE: The white barrel of the lens uses a new technology to better reflect infrared and keep the barrel cooler. Can you share any further details on this? What is it that makes the underlayer IR-reflective? Do you know if this approach is unique to Olympus, or do others use a similar two-layer design? I was also a little confused about the statement that it reduces internal temperature rise by 10% and external by 30%. What do internal and external mean in this context? (Also, we always talk about temperature rise being an problem with big teles, but I assume that there could be a similar issue if lenses get very cold, as might occur in wildlife shooting. Is that the case? - If so, I'd imagine that it would be a good idea for wildlife photographers to somehow insulate and/or warm their lenses in very cold conditions; is that true?)
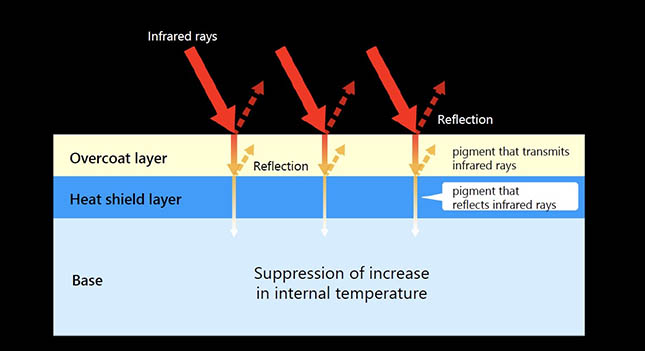
OM: The "external temperature" refers to the surface temperature of the white-color exterior, and the "internal temperature" refers to the temperature of the space inside the lens barrel. We cannot give you detailed information about the specific mechanism of infrared reflection. We do not know the approaches of other companies, but we have adopted a new coating for this product that is optimal for its thermal barrier effect and reliability in terms of strength, etc.
For example, if the internal temperature of the lens rises only locally (only in a specific area), in the area that is exposed to direct sunlight, the distance between the lens elements will change slightly due to the thermal expansion only in that area, which may cause a change in spherical aberration (although I think this will actually have little effect on image quality). In order to minimize the impact on image quality, the lens is painted white to suppress the rise in surface temperature and to prevent a large difference in surface temperature between areas exposed to direct sunlight and areas in the shadows.
It is the same for cooling. By preventing temperature unevenness from occurring, the effect on image quality is minimized. This product, like all PRO lenses, has a -10°C low-temperature resistance, ensuring stable optical performance even in harsh environments such as in snow.
I was disappointed that they couldn't share any details about the IR-reflective coating. I knew that the point of white lens barrels was to help keep them cooler when the sun's beating down, but this was the first time I'd heard of a separate, specifically IR-reflective layer. From the presentation, it seems that the IR-reflecting layer is under the white paint. I wonder what it looks like?
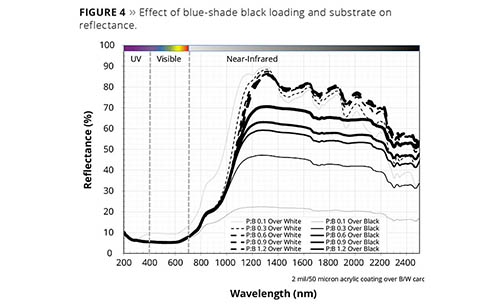
(Illustration taken from here.)
I did a little Googling about IR-reflective pigments, and it seems that they're usually made from various metal oxides. Some of the best apparently look nearly black in the visible range. So it makes sense that Olympus used two layers, a top layer that reflected visible light but let the IR pass through, and an undercoating that just reflected the IR. (Interestingly, some of the articles I read pointed out the importance of the top layer allowing IR to pass through it, vs absorbing it. Some paints that look white in the visible spectrum actually absorb infrared, which would heat up the lens barrel and defeat the whole purpose.)
-- Lens thinning technology
DE: Another technology that was mentioned in the presentation was "lens thinning technology", mentioned as part of the discussion of AF speed. What is meant by lens thinning technology, and what are the keys to it? Does it have to do with being able to mold very thin lens sections when making aspheric lenses? Or is it a matter of being able to grind and polish such delicate sections conventionally?
OM: In order for a super-telephoto zoom lens to drive the AF quickly and quietly, the lens group that controls the AF (hereinafter referred to as "the focus lens group") needs to be lightweight. From the very beginning of the design process, we considered and incorporated a configuration that would reduce the volume of this lens group and make it lighter. As part of this, the lens elements actually used in the focus lens group are polished to the utmost thinness while ensuring high precision, to achieve a lightweight focus lens group.
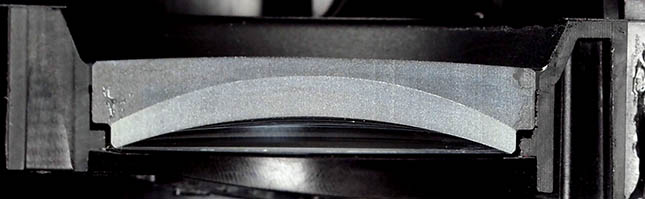
Many people don't realize that all the glass in a lens element that's between its two surfaces doesn't actually serve any purpose, other than to keep those surfaces in their places. The only part of the lens element that does any work in actually bending the light is a microscopically-thin layer right at the surface; everything else is just along for the ride. (This is the basis of Fresnel lenses, first used for crafting massive lighthouse optics.)
As the engineers said, a key to AF speed is making the focus group as lightweight as possible. This means you'll want to polish the elements down as thin as possible, to save on mass. Of course, the thinner you make a lens, the more delicate it becomes, so it takes very careful handling throughout the grinding and polishing process to avoid cracking it. It's easy to see in the optical formula for the 150-400mm which lens is likely the most problematic, the very thin meniscus element that's on top in the image above. Some of the other elements in the lens appear similarly thin, but it seems that this one in the focus group was a particular ... uh, "focus" ... of the engineers' attention. (Sorry, I couldn't resist ;-)
-- Other tuning for AF speed
DE: The presentation also mentioned "tuning other parameters" to AF speeds faster than the 300mm. What did this consist of?
OM: We designed this lens to exceed the 300mm PRO lens in AF speed.
To make AF speed faster, lighter weight of the focus lens unit and a short moving distance of the unit are important. There are many parameters related to these that we needed to consider for making AF speed faster. For example, not just the weight of the lens unit, but also stroke distance, the weight of the parts supporting lens elements, stiffness of materials, moving speed of the lens unit, positioning accuracy and so on. All of them must be balanced. To find the best balance, multiple teams working with different responsibilities worked closely from early stages of the design.
There are trade-offs though. When shortening the moving distance of the focus lens unit, higher positioning accuracy is required. To achieve the required accuracy level, we developed a new moving mechanism and control system.
Additionally, we tested prototypes to tune the control carefully, to realize both a high level of positioning accuracy as well as fast AF speed.
Depending on specific shooting situations, we realized a 20% faster AF speed than M.Zuiko 300mm F4 PRO lens, based on modeling projections.
As you can tell from their reply here, there are a lot of factors involved in making an AF system as fast and responsive as possible. I'd been aware of most areas they mentioned previously, but this was the first time I'd heard engineers mention the stiffness of materials as an area of concern. It makes sense of course; if you're trying to shove the AF elements back and forth as quickly as possible, the support structures could flex somewhat, especially if you're also trying to thin those structures down as much as possible to reduce their weight. While obvious in hindsight, this had never occurred to me as something you'd need to think about, and this was the first time I'd heard it mentioned specifically by lens engineers.
There's a lot to unpack in their reply, that touches on pretty much every element of AF speed (apart from the actuators, which I found interesting that they didn't mention; I guess that either wasn't a limiting factor in their design, or their technology in that area was already at its limit.)
As noted, AF speed is all about moving the focus group as rapidly as possible. We've already talked about their efforts to reduce the weight of the lens group as much as possible, so the actuator system can move it quickly, but another aspect is reducing the distance that you have to move it. Obviously, for a given maximum speed, moving the focus group 1 mm will take less time than as if you had to move it 2 mm. So one way to get higher AF speeds is to design the optical formula so the focus group has to move as short a distance as possible, to shift from infinity to closest focus.
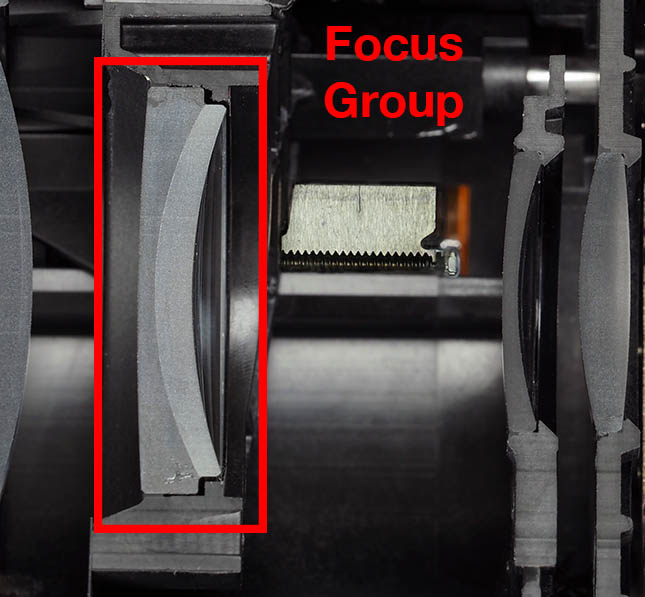
That's great, but it quickly leads to another problem: The smaller the distance you have to move the focus group, the more precisely you'll need to position it. If the focus group of one lens has to move, say, 10mm to go from infinity to minimum focus and another only has to move 1mm, that means you'll need to position the second one 10x more precisely than the first. As is always the case in engineering, there's a trade-off to be made, and you need to work the problem from both sides. With the 150-400mm, they said that they had to develop both a new mechanism and control system.
Possibly the most interesting insight here is the reference to separate teams that worked on different parts of the problem independently. Again, this makes sense, but it gives an idea of just how much goes into pushing the state of the art of lens technology. It's not just a matter of coming up with a particular optical formula, but using the example of this lens, there were likely teams focusing on aspheric molding of ED glass, weight reduction and rigidity of the mechanical components and increasing the precision of the position-feedback for the focus group. On top of all that, firmware engineers had to work to tweak the feedback loops that control the whole thing. Again, while I'd always vaguely assumed that there'd be multiple engineers involved in a lens design, this discussion gave me a broader picture of the magnitude of the effort.
-- What's up with the crazy-expensive protection filter? (Actually, not so crazy...)
DE: The protection filter is very expensive ($325 in the US!) What's the reason for that? I think it also has a nano-AR coating, is that part of it? (Or is the ZERO coating the presentation referred to for it different than the Z-coating mentioned earlier?) My understanding has always been that nano coatings are very delicate and susceptible to scratching. If there is a nano coating on it, how is it able to withstand normal handling?
OM: The coating used for this protection filter is a combination of ZERO coating and an anti-dust coating; the Z Coating Nano is not used.
With a larger-diameter protection filter, it is more difficult to maintain the flatness of the glass, and the accuracy influences optical performance. So, we were required to pay close attention to develop this 95mm-diameter protective filter with very high flatness level uniformly across the entire surface. We have confirmed that this filter can deliver the best performance with the 150-400mm PRO lens with our in-house tests.
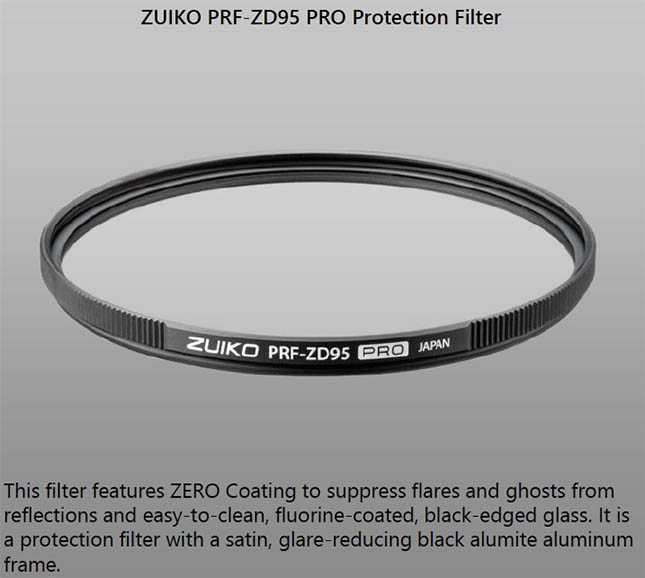
A lot of photographers treat filters as afterthoughts; after all, they're just bits of flat glass, right? While the ZD95PRO's $325 price initially struck me as well on the high side, a quick Google search while writing this article showed that it's actually very much in line with other high-quality 95mm-diameter filters. A 95mm UV filter from Zeiss is currently running $396 here in the US, one from Leica is going for $375, and even high-end Tiffen models range from $327 to $336. So $325 for a high-quality, super-flat and well-coated protective filter from Olympus is very much in line with the rest of the market.
The OM Digital engineers called attention to its flatness, uniformity and coating, all of which are important. As I mentioned, we tend to dismiss filters as trivial chunks of glass, but the fact is, anything that gets between the sensor and your subject is part of the optical chain. You could have the best AR coatings in the world on your lens, but if you stick a filter with bad coatings on the front of it, you're going to boost flare and cut local contrast. Any variations from dead-flat and any variations in thickness are going to translate into subtle optical distortions as well, as the light makes its way through the filter and then the lens.
My personal reference point for filters had been much smaller-diameter ones, up to maybe 72mm or so, which are naturally much less expensive. Just in terms of area, there's 75% more glass in a 95mm filter than in a 72mm one. And cost doesn't just scale linearly either; larger-diameter blanks of optical glass are more expensive than smaller ones, by more than just the ratio of area.
So bottom line, while my initial reaction was that the $325 price of the ZD95PRO filter was high, it's well-justified and very much in-line with similar high-end products from other manufacturers. - And I'd much rather have to replace a $325 filter than shell out whatever the repair cost might be for the front element of the 150-400mm itself :-)
Summary
I love the conversations I have with camera and lens engineers; it's endlessly fascinating to me to hear about the challenges they face in their work and how they managed to overcome them. The M.Zuiko 150-400mm F4.5 IS PRO is a true landmark in lens design, with a remarkable combination of zoom reach, optical quality, image stabilization performance, weather resistance and compact, lightweight portability. It's a powerful example of the benefits that Micro Four Thirds systems from the newly-named OM Digital Solutions Corporation bring. Every system has its particular advantages, and there are certainly areas where full-frame cameras will carry the day. If you're a wildlife or sports shooter, though, it's hard to argue with the sheer optical quality and zoom reach that the OM Digital 150-400mm PRO provides, in an extraordinarily compact, lightweight and highly weather-resistant package. As I said at the outset, it actually looks like a bargain, even at its lofty $7,500 selling price.
Sponsored content notice: This article was sponsored by OM Digital Solutions Corporation, but our questions, comments and analysis are our own. (The only edits OM Digital requested for our content involved making sure that we used the correct branding for the lens itself and OM Digital as a company.) As always, I really appreciate OM Digital making their engineers available for such in-depth questioning and discussion!